Flexible Foam Manufacturers Near Domlur
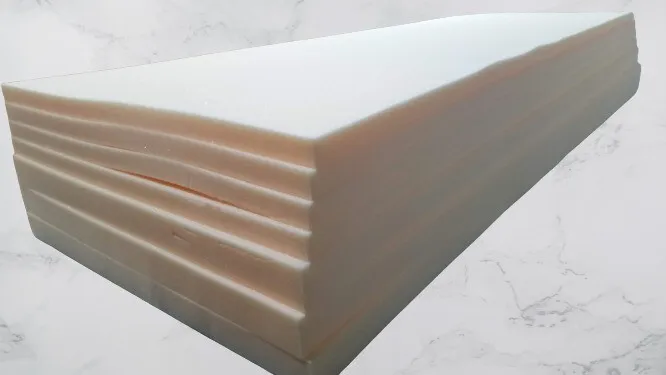
Contact : +91 91106 81734
Flexible Foam Manufacturing
Introduction
Flexible foam is a versatile material used across various industries, including automotive, furniture, bedding, and packaging. Its properties, such as cushioning, insulation, and sound absorption, make it a popular choice for applications requiring both comfort and support. The manufacturing process of flexible foam involves several key stages, each crucial to producing a high-quality product.
1. Raw Materials
The primary raw materials for flexible foam manufacturing are polyols and isocyanates, which are combined to create polyurethane foam. Polyols are alcohols with multiple hydroxyl groups, and isocyanates are reactive chemicals that form urethane bonds when combined with polyols. Additives, such as catalysts, surfactants, and flame retardants, are also used to modify the properties of the foam.
2. Chemical Reaction and Foam Formation
The process begins with the mixing of polyols and isocyanates in specific proportions. This reaction occurs in a high-speed mixer, where the components are blended with additives to achieve the desired characteristics of the foam. The chemical reaction between polyols and isocyanates produces polyurethane foam through a process known as polymerization.
In this process, the foam is created by introducing a blowing agent, which causes the mixture to expand and form bubbles. The blowing agent can be a physical agent, like carbon dioxide, or a chemical agent, like water. As the foam expands, it begins to set, forming a cellular structure with numerous tiny air pockets. This structure gives the foam its flexibility and cushioning properties.
3. Molding and Curing
Once the foam mixture is prepared, it is poured into molds to shape it according to specific requirements. The molds are designed to create foam products of various sizes and shapes, from large sheets to custom-designed cushions. The mixture is allowed to expand and cure within the mold, solidifying into its final form.
Curing is a crucial step that involves maintaining the foam at a controlled temperature and humidity for a specific period. This allows the chemical reactions to complete and the foam to achieve its final strength and flexibility. The curing process can vary depending on the type of foam and its intended application.
4. Cutting and Shaping
After curing, the foam is removed from the molds and subjected to cutting and shaping processes. This step involves trimming excess material and cutting the foam into the desired dimensions. Specialized equipment, such as hot wire cutters or bandsaws, is used to achieve precise cuts and shapes.
The cutting and shaping processes are essential for ensuring that the foam products meet the specifications required for their intended use. This step also includes any additional processes, such as contouring or profiling, to enhance the foam's performance and appearance.
5. Quality Control
Quality control is a critical aspect of flexible foam manufacturing. Various tests are conducted to ensure that the foam meets the required standards for properties such as density, firmness, resilience, and durability. Tests may include:
- Density Measurement: Determines the mass of the foam per unit volume, which affects its cushioning properties.
- Compression Testing: Assesses the foam's ability to withstand compressive forces and return to its original shape.
- Tensile Testing: Measures the foam's strength and elasticity under stretching forces.
- Flammability Testing: Ensures that the foam meets safety standards for fire resistance.
Quality control ensures that the foam products are consistent and reliable, meeting both industry standards and customer expectations.
6. Applications and Uses
Flexible foam is used in a wide range of applications due to its adaptability and performance characteristics. Some common uses include:
- Furniture: Cushions and upholstery in sofas, chairs, and mattresses.
- Automotive: Seat padding, headrests, and insulation materials.
- Bedding: Mattresses and mattress toppers.
- Packaging: Protective packaging for fragile items.
- Acoustics: Soundproofing materials for walls and ceilings.
Each application may require specific formulations and properties of foam, leading to variations in the manufacturing process to meet different needs.
7. Environmental Considerations
Environmental concerns are becoming increasingly important in flexible foam manufacturing. The industry is focusing on reducing the environmental impact through several measures:
- Recycling: Foam recycling programs and the use of recycled materials in production.
- Sustainable Materials: Development of bio-based or renewable raw materials.
- Energy Efficiency: Implementing energy-efficient processes and technologies to reduce carbon footprint.
Efforts to minimize environmental impact are vital for the sustainability of the foam manufacturing industry and contribute to broader environmental goals.