Customized Foam Size Suppliers Near Hebbal
- 4 months ago
- Customized Foam Size Suppliers Near Hebbal ,
- Memory Foam Dealers Near Banashankari ,
- Best Latex Foam Dealers Near Hebbal ,
- High-Density Foam Dealers In Jayanagar ,
- Flexible Foam Manufacturers Near Bommanahalli ,
- Customized Foam Size Dealers In Whitefield
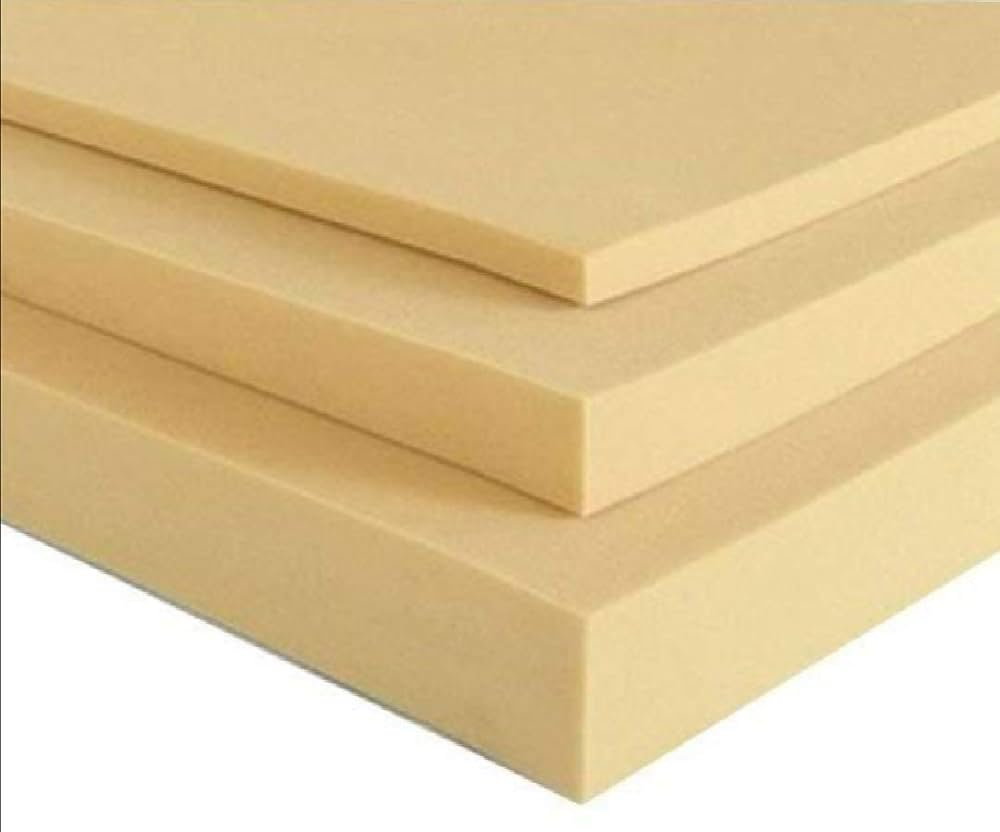
Contact : +91 91106 81734
Customized foam size refers to the process of tailoring foam products to meet specific dimensions and requirements for a variety of applications. This customization ensures that foam fits perfectly into its intended use, whether it's for packaging, cushioning, insulation, or other purposes. Here’s an overview of what customized foam size entails, its benefits, and its applications.
What is Customized Foam Size?
Customized foam size involves creating foam products with specific dimensions and characteristics based on the user's needs. Foam can be cut, shaped, and sized to fit particular objects or spaces, ensuring optimal performance and efficiency. This process often involves selecting the right type of foam material, determining the exact dimensions, and applying the appropriate manufacturing techniques.
Types of Foam Materials
-
Polyurethane Foam: Known for its versatility and cushioning properties, polyurethane foam is commonly used in furniture, bedding, and packaging. It can be customized in various densities and firmness levels.
-
Memory Foam: This type of foam conforms to the shape of an object or body, making it ideal for ergonomic applications like mattresses and cushions. Memory foam customization involves tailoring the thickness and density to achieve the desired comfort level.
-
Polyethylene Foam: Durable and resistant to moisture, polyethylene foam is often used in packaging and insulation. Custom sizes can be created for specific packaging needs or to fit into tight spaces.
-
EVA Foam: Ethylene-vinyl acetate (EVA) foam is flexible and resilient, often used in sports equipment, safety mats, and craft projects. Custom EVA foam products can be shaped for specific uses, such as protective gear or flooring.
Benefits of Customized Foam Size
-
Enhanced Protection: Custom-sized foam provides a perfect fit for items being packed or transported, reducing the risk of damage during handling and transit. It’s especially useful for delicate or high-value items.
-
Improved Comfort: In applications like mattresses and cushions, customizing foam size allows for optimal comfort and support, tailored to individual preferences or requirements.
-
Efficient Use of Space: Custom foam can be designed to fit precisely into designated spaces, making efficient use of available space and improving the overall organization.
-
Cost-Effectiveness: By customizing foam to fit specific dimensions, companies can reduce waste and avoid overproduction, ultimately leading to cost savings.
Applications of Customized Foam Size
-
Packaging: Customized foam inserts are used to protect products during shipping. Foam can be cut to fit around electronic devices, fragile items, or custom-shaped goods to prevent movement and damage.
-
Bedding and Furniture: Custom-sized foam is used in mattresses, pillows, and upholstered furniture to provide the right level of support and comfort. Manufacturers often tailor foam dimensions to fit different bed sizes and furniture designs.
-
Automotive: In the automotive industry, foam is used for insulation, soundproofing, and padding. Custom foam pieces can be designed to fit specific parts of a vehicle, enhancing performance and comfort.
-
Construction and Insulation: Foam is used in building insulation to maintain energy efficiency. Custom-sized foam boards or panels can be tailored to fit various spaces, ensuring effective thermal insulation.
-
Sports and Recreation: Foam is used in sports equipment, safety mats, and protective gear. Customization allows for tailored shapes and sizes to meet specific safety standards and user needs.
Manufacturing Process
The process of creating customized foam size typically involves several steps:
-
Design and Measurement: Determine the exact dimensions and specifications required for the foam product. This may involve measuring the item to be protected or the space where the foam will be used.
-
Material Selection: Choose the appropriate type of foam based on the application. Different foams have unique properties, such as density, firmness, and flexibility.
-
Cutting and Shaping: Foam is cut and shaped using specialized tools and machinery. Techniques such as CNC cutting, die-cutting, or water jet cutting may be employed to achieve precise dimensions.
-
Testing and Quality Control: Customized foam products are tested to ensure they meet the required specifications and quality standards. This step helps ensure that the foam performs as expected in its intended application.
-
Final Adjustments: Any necessary adjustments are made to the foam size or shape before the final product is delivered.
Conclusion
Customized foam size offers a range of benefits across various industries, providing tailored solutions for protection, comfort, and efficiency. By selecting the right type of foam and customizing it to specific dimensions, users can achieve optimal performance and meet their unique needs. Whether for packaging, bedding, automotive applications, or construction, customized foam plays a crucial role in enhancing both functionality and user experience.